塗装方法別の推奨膜厚と膜厚のコントロール方法
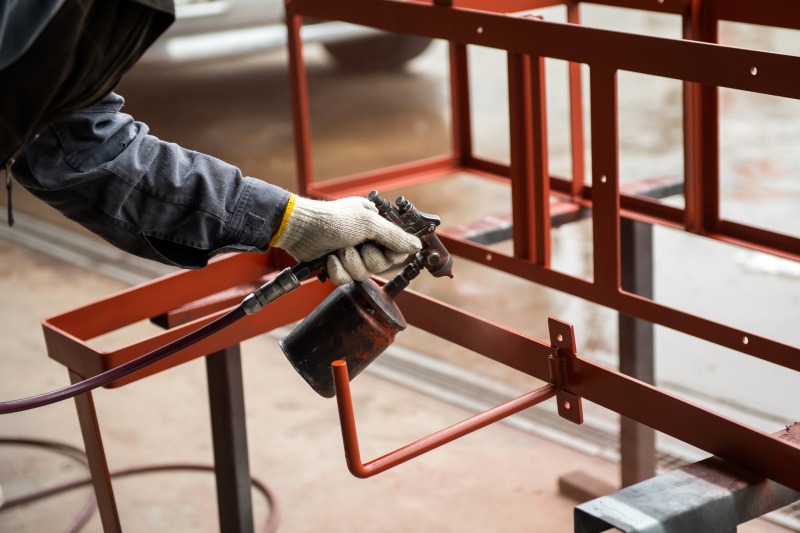
近年、工業製品の品質向上と環境規制の厳格化に伴い、塗装技術はますます高度化しています。本稿では、主要な塗装方法の特徴と推奨膜厚、そしてカチオン電着塗装における膜厚コントロールの重要性について解説します。
各塗装方法の特徴と推奨膜厚
1. カチオン電着塗装(15~25μm)
カチオン電着塗装は、被塗装物を導電性水性塗料中に浸漬し直流電流を流すことで、被塗装物に塗膜を析出させる塗装方法です。15~35μmという比較的薄い膜厚でも優れた防錆性を発揮し、特に自動車のボディや部品の下地塗装として重要な役割を果たしています。
複雑な形状の部品でも均一な塗膜を形成できる特長があり、量産品の品質安定化に大きく貢献しています。また、環境負荷が低く、塗着効率が高いことから、製造コストの最適化にも寄与しています。
2. 吹付塗装(20~60μm)
最も一般的な塗装方法の一つである吹付塗装は、その多用途性の高さから幅広い産業で使用されています。エアガンによる塗料の微粒化により、20~60μmの範囲で膜厚をコントロールできます。
建築内装や家具、自動車補修など、美観が重視される用途に適しており、熟練した技術者の手によって高品質な仕上がりを実現できます。ただし、オーバースプレーによる塗料のロスや、作業環境への配慮が必要という課題もあります。
3. 粉体塗装(50~100μm)
環境配慮型の塗装方法として注目を集める粉体塗装は、有害物質を含む溶剤を使用しない特徴があります。50~100μmという比較的厚い膜厚により、優れた耐久性と防食性を実現します。
特に屋外設備や耐久性が求められる製品に適していますが、高温での焼付けが必要なため、熱に弱い素材には適用できないという制限があります。一方で、塗料の回収・再利用が可能なため、材料効率が高いという利点があります。
4. 静電塗装(30~80μm)
静電塗装は、塗料粒子を帯電させて被塗装物に吸着させる方式で、30~80μmの膜厚範囲で管理されます。塗着効率が高く、複雑な形状の製品でも均一な塗膜を形成できる特長があります。
自動車や電化製品など、大量生産品の塗装に適しており、材料ロスが少ないことから、コスト効率の面でも優れています。ただし、設備投資が必要で、導電性の被塗装物に限られるという制約があります。
5. 溶剤塗装(20~40μm)
従来から広く使用されている溶剤塗装は、20~40μmの比較的薄い膜厚で美しい光沢を実現できます。速乾性があり、多様な色や仕上げに対応できる柔軟性が特長です。
しかし、VOC(揮発性有機化合物)の排出という環境面での課題があり、作業環境の換気対策が不可欠です。近年は環境規制の強化に伴い、水性塗料への転換が進んでいます。
カチオン電着塗装における膜厚コントロール方法
カチオン電着塗装の品質管理において、膜厚コントロールは極めて重要です。以下に主要な制御パラメータとその影響について詳述します。
タクト(浸漬時間)の管理
浸漬時間は塗膜析出の基本要素です。長過ぎると塗膜のムラや異常析出の原因となり、短過ぎると必要な膜厚が得られません。最適なタクトタイムは、製品の形状や要求される品質仕様によって異なります。
温度管理
塗料槽の温度は、塗料の粘度に直接影響を与えます。一定の温度で管理され、温度が高いと塗膜が厚くなり、低いと薄くなる傾向があります。また、焼付け温度も最終的な膜厚に影響を与えるため、適切な温度設定が重要です。
電圧の最適化
電圧は塗料粒子の電着力を決定する重要なパラメータです。低過ぎると十分な膜厚が得られず、高過ぎると異常析出やピンホールの原因となります。一定の電圧で管理され、製品の形状や大きさ、材質に応じて最適化が必要です。
溶剤比率の管理
塗料中の溶剤比率は、最終的な膜厚に大きく影響します。溶剤比率が高いと膜厚が厚くなり、低いと膜厚が薄くなる傾向があります。定期的な濃度管理と適切な補給が不可欠です。
各塗装方法には、それぞれ特有の推奨膜厚範囲があり、用途や要求品質に応じて適切な選択が必要です。特にカチオン電着塗装においては、複数のパラメータを総合的に管理することで、安定した品質の塗膜を形成することができます。
今後は、環境負荷の低減と品質向上の両立がさらに求められる中で、これらの塗装技術はさらなる進化を遂げていくことが予想されます。製造現場では、これらの基本原理を十分に理解した上で、最適な塗装条件を見出していくことが重要です。